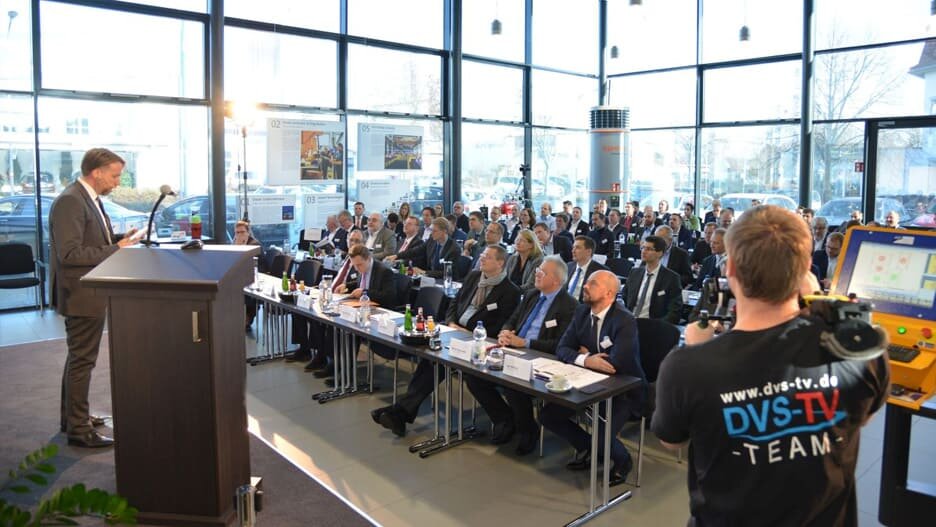
Creating the digital transformation
Published in "Der Praktiker" - the magazine for welding technology and more.
by Dr. Michael Schnick, Klipphausen, Volker Krink, Finsterwalde, Dr.-Ing. Konstantin Kernschmidt, Igor Mikulina, Matthäus Mikulina, Bad Wörishofen
Everyone is talking about digitization: people, machines, logistics and products are to be intelligently networked. To ensure that small and medium-sized companies can also benefit from these trends, machine manufacturers are in demand. Through cross-manufacturer collaboration, they can offer holistic solutions that enable the digitization of manufacturing and deliver immediate, tangible added value to the manufacturing operator.
SMEs on the way to "Industry 4.0
The digitization of production is a current megatrend. On the one hand, it meets the demands of market dynamization, for example the increase in product variants with simultaneously decreasing batch sizes and higher production flexibility (market pull). On the other hand, it is driven by the new possibilities of computer and network technology as well as data processing and artificial intelligence (technology push). For producers, the 4th industrial revolution holds out the prospect of significant increases in productivity coupled with rising production complexity. Machine and plant manufacturers want to profit in the future through new differentiation features, intensified customer loyalty, and by securing and expanding aftersales and digital service.
Here, "Industry 4.0" clearly goes beyond the 3rd industrial revolution, automation through computer technologies, also called "Automation 3.0". The basic idea is that the information and data do not remain in a kind of "data silo" at the machine, but are made available to every hardware and software in the company network. In contrast to automation, sensor data is therefore not only used at the machine or plant where this information is generated, but also enables new functions and added value at other machine systems, at or through company software, and at automation levels above the fieldbus and control (PLC) level. To achieve this, it is essential that all machines are able to communicate with each other securely and seamlessly. In the future, this communication interface and the services that build on it will form an important field of properties for product differentiation in addition to the unique technical features. At the same time, the communication interfaces are a prerequisite for finding an optimum of the production processes for the current boundary conditions in the digital model, the so-called "digital twin", and transferring this to the control system of the "smart factory".
The "Smart Factory" in medium-sized companies
The digital transformation of medium-sized manufacturing operations into so-called "smart factories" involves many facets. Especially because the world of small and medium-sized enterprises (SMEs) is so diverse, the machines, logistics systems, production processes and software systems used differ from factory to factory. The basis of the "smart factory" are the so-called "assets" that are to be networked with each other. These can be machines, devices or components in the factory, for example. However, other areas of the company, such as building control or access control, or processes outside the company, such as suppliers, can also be included.
The aim is to use digitization and networking to increase key competitive factors, such as flexibility, on-time delivery, quality, and customer satisfaction, and to enable new, innovative business models.
Structure and scope of the digital network of a smart factory
Creating the conditions for the "Smart Factory
Before the advantages of a "smart factory" can be used, computerization and networking of all machines in the factory must be in place. In most cases, modern machines already have a digital control system (for example, programmable logic controllers (PLCs), computer numerical controls (CNCs)) that reads the sensor data and controls the actuators. However, many companies also use machines that are decades old and still perform well. Such machines must be modernized with suitable retrofit solutions so that at least basic data is available in digital form.
Step by step to "Industry 4.0" (based on acatech study: Industry 4.0 Maturity Index)
In order to be able to use the data of all machines and equipment in a "smart factory", they must have suitable connectivity. Classically, fieldbus systems are used today in automation technology for production control. These are used, for example, to control the production process or coordinate the interaction of several machines. However, the disadvantages of many of these bus systems for the "smart factory" lie in their closed architecture, the lack of interoperability of different systems (interoperability = ability to work together seamlessly), and the capacity limitations for the enormously growing volume of data. For a "Smart Factory", open interfaces, for example OPC UA, must therefore be used on the machines and systems. If the existing control systems are not to be adapted for this purpose, or if they do not have the required computing power, it is advisable to use external gateways (switching devices in computer networks) with appropriate protocol adapters that read out the control data, process it into relevant information and make it available to the "Smart Factory". However, with some solutions for hardware gateways available on the market, it should be noted that these do read out the sensor data, but then forward it to their own cloud, where it is made available to the customer. Since this cloud is not in the hands of the customer, but in the hands of the gateway provider, such a solution leads to an undesired dependence on the cloud and significantly restricts flexibility.
See the present, understand the past, predict the future
If these prerequisites have been created in the company, the first added values already become apparent through the digital image of production, which is up-to-date at all times. This new perspective provides a transparent picture of causes and their effects. Compared to stand-alone solutions, it is crucial that visibility and transparency encompass all digitally connected machines. For example, factory operators can see the upcoming maintenance dates of all their machines at a glance. He is thus spared the previously necessary consolidation of individual data and manual administration. By cleverly planning and combining maintenance, unnecessary production downtimes can be avoided.
If, in the next step, additional intelligence is used to create the ability to analyze production and make reliable predictions, considerable efficiency gains can be achieved. Companies are thus in a position to make decisions in good time or to initiate necessary reaction measures at an early stage. For example, the necessary time for a gas delivery can be determined on the basis of current consumption, or the end customer can be alerted at an early stage to a delay in his components due to a production problem.
The last step describes the future vision of a "smart factory" with self-organizing production resources that support production control as assistance systems and can react to changing boundary conditions. If the prerequisites already described here are created, a certain degree of autonomy can already be implemented in production today. Depending on machine complexity and availability, for example, repairs can be automatically requested in the event of a machine failure, the production process can be shifted to other machines, and a change in the production sequence can be suggested or made directly.
Thus, intelligent, cross-manufacturer networking of production offers a level of transparency not previously available and thus forms the basis for producing efficiently, saving resources and controlling the company. But most importantly: This enables SMEs to secure competitiveness in the future despite decreasing batch sizes and increasing international competition.
Application example plasma cutting machine
In order to be able to integrate new machines directly into a "smart factory" in the future without great effort, their connectivity and digital data availability are an essential prerequisite. This is illustrated below using the example of a plasma cutting machine, and the application benefits and added value of additional digital services are described.
Plasma cutting machines, in conjunction with a CNC flame cutting machine and appropriate extraction systems, allow the cutting of metals in the sheet thickness range from 0.5 mm to 160 mm. Modern plasma cutting machines stand for high cutting speeds and an almost post-processing-free cut. In addition to the cost of the plasma system and wearing parts, the cut quality and cutting speed are conventional product differentiators. With the plasma cutting systems of the new "Q-series" these are considerably extended by digital property fields.
In the new "Q 3000", for example, the machine as well as the gas box and the burner connection unit are equipped with microcontrollers that recognize each other and provide process and status key figures for the central control system. The latter uses the data in a model for internal analyses and stores the data in a database. Among other things, the control system calculates the remaining service life of electrical components and the plasma system, totals electricity and gas consumption, and can infer possible operating errors. The information is either passed on to the CNC machine (to a lesser extent) via the "EtherCAT" field bus system or can be retrieved from the network via Ethernet. Three communication levels were designed here.
Communication levels of a plasma cutting system
The operator interface aims to support the machine operator. The information is provided by a web application that can be called up or made visible via various end devices, for example tablet, personal computer or cell phone, using a web browser. Among other things, parameter sets are assigned to different cutting tasks and the wear parts to be fitted for these are clearly named and visualized. The web application also stores operating documents and videos for troubleshooting, as well as maintenance and operating instructions, and links them to machine error messages. The power and gas consumption can be tracked using a calendar function.
The information can also be made available to the machine network. There, for example, the information on the maintenance status and remaining service life of the CNC flame cutting machine can be integrated into the predictive maintenance functions of the entire plant. On the other hand, condition data from the machine can be used directly to control other machines, for example extraction machines or ventilation systems to reduce electricity and heating costs. Finally, information on electricity and gas consumption can be clearly assigned to cost centers or products, enabling more precise monitoring of machine costs (total cost of ownership) and product-related manufacturing costs.
Ultimately, a connection can be established with the machine manufacturer's customer service department using a router integrated in the machine and with the express consent of the machine operator. The latter has the options online and without additional travel costs:
- monitor the process or the functionality of the machine together with the plant operator,
- analyze any application problems that arise, right down to the internal communication of the plasma cutting system, and make adjustments,
- update the software status, for example, to install new help videos and tutorials with software updates or parameter adjustments to extend the service life of wear parts.
"Industry 4.0" - from SMEs for SMEs
"Industry 4.0" offers considerable opportunities for SMEs in particular, even in global competition, through cross-manufacturer collaboration. Nevertheless, 80% of all SMEs in Europe have not yet taken any comprehensive steps to drive forward networking in their own production or that of their products. This is mainly due to the fear of high costs, dependence on one supplier and a lack of capacity to deal with the topic in detail. In addition, many SMEs do not have a specified implementation strategy and are in danger of losing out in the international digitization race.
The Industry Business Network 4.0 e. V. association was founded in 2016 to support medium-sized companies in the digitization of their products and production and to jointly develop cross-manufacturer solutions with tangible added value for customers. In addition to medium-sized manufacturers from the mechanical and plant engineering sector, TÜV Süd and Fraunhofer IGCV are among the founding members and make their expertise and consulting services available to the members. In the association, numerous technology-leading machine manufacturers, service providers and users are working on developing products for "Industry 4.0" and testing them on real reference plants in technology centers and in production. With the "IndustryFusion" initiative launched for this purpose, the association is making open, cross-vendor and seamless networking - the core idea of "Industry 4.0" - a reality. Based on a cross-manufacturer open source networking solution for "Smart Factories", "IndustryFusion" enables seamless linking of machine, factory and, if necessary, cloud platforms. The simplicity of implementation is a central component of the solution and thus enables SMEs in particular to take advantage of a broad "Industry 4.0" ecosystem.
The first important milestone was presented at the "EuroBlech" 2018 trade fair in Hanover. True to the trade show motto "On the pulse of digitization," more than 20 different machines and devices from various manufacturers were networked across several trade show booths and their information, for example regarding machine status, energy consumption and maintenance, was seamlessly exchanged with each other and transparently presented to visitors. At the association's headquarters in Bad Wörishofen, Bavaria, the association's first permanent reference plant was then put into operation as part of the "Manufacturing 4.0" trade congress, and is constantly evolving in the sense of a living demonstrator. The association is currently setting up further reference plants with different machine and software constellations at various locations in Europe. The network thus created can be used by members, but also by interested companies, to keep abreast of progress and to play an active role in implementing "Industry 4.0" from SMEs for SMEs.
Presentation of the digital reference plant at the "Manufacturing 4.0" trade congress
In order to demonstrate the performance and sustainability of open manufacturing networking in real production, the association is also implementing its solution in a reference project at a very innovative Swiss steel trader with six manufacturing sites by the end of 2020. The special innovation factor of the project lies in the collaboration of all machine manufacturers involved, IT experts from the open source sector, providers of software solutions for the user, and the operator of the manufacturing facility. Together, value-added application examples are defined, data to be exchanged is determined and new types of digital services are tested. This creates a win-win situation for all participants, which can also be applied to the other association members' own products.
In all implementations of "Industry 4.0", it is also important to consider more than just the technical aspects. The Industry Business Network 4.0 e. V. association therefore also supports its members with suitable guides in preparing for the digital transformation in their own companies and by imparting knowledge regarding suitable use cases and new business models.
This article first appeared in the magazine "Der Praktiker", issue 8/2019. Here it goes to the Website
Authors:
- Dr. Michael Schnick, Managing Director, Oscar PLT GmbH
- Volker Krink, Head of Development, Kjellberg Technologiepark GmbH
- Dr.-Ing. Konstantin Kernschmidt, Head of Research and Development, MicroStep Europa GmbH
- Igor Mikulina, Managing Director MicroStep Europe and Chairman of the Board Industry Business Network 4.0 e.V.
- Matthäus Mikulina, Business Development Industry 4.0, MicroStep Europa GmbH