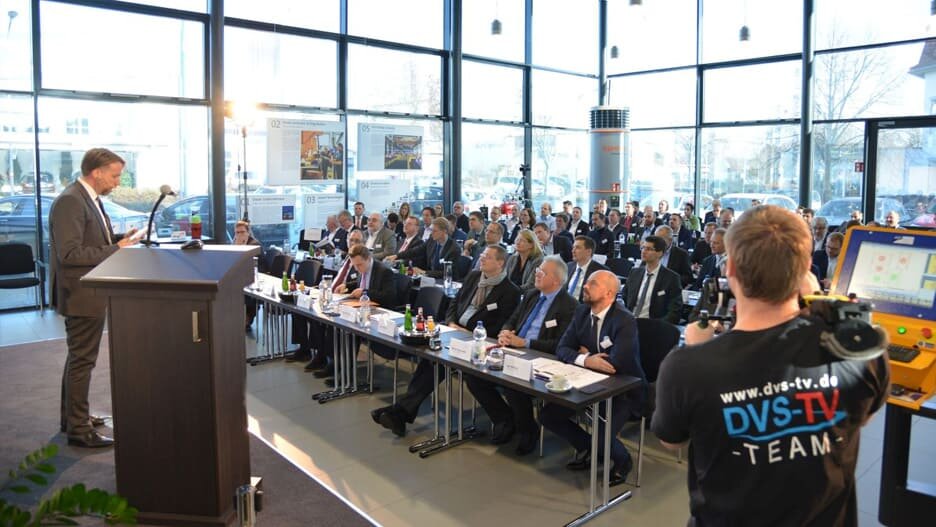
Die digitale Transformation schaffen
Publiziert in „Der Praktiker“ - das Magazin für Schweißtechnik und mehr.
von Dr. Michael Schnick, Klipphausen, Volker Krink, Finsterwalde, Dr.-Ing. Konstantin Kernschmidt, Igor Mikulina, Matthäus Mikulina, Bad Wörishofen
Die Digitalisierung ist in aller Munde: Menschen, Maschinen, Logistik und Produkte sollen intelligent miteinander vernetzt werden. Damit auch kleinere und mittlere Unternehmen von diesen Trends profitieren können, sind die Maschinenhersteller gefragt. Durch herstellerübergreifende Zusammenarbeit können sie ganzheitliche Lösungen bieten, die eine Digitalisierung der Fertigung ermöglichen und dem Fertigungsbetreiber sofort greifbare Mehrwerte liefern.
Der Mittelstand auf dem Weg zu “Industrie 4.0”
Die Digitalisierung der Produktion ist ein aktueller Megatrend. Sie entspricht zum einen den Forderungen der Marktdynamisierung, zum Beispiel dem Anstieg der Produktvarianten bei gleichzeitig sinkenden Losgrößen und höherer Produktionsflexibilität (Market Pull). Zum anderen wird diese vorangetrieben durch die neuen Möglichkeiten der Computer- und Netzwerktechnik sowie der Datenverarbeitung und der künstlichen Intelligenz (Technology Push). Produzenten stellt die 4. industrielle Revolution deutliche Produktivitätssteigerungen bei gleichzeitig steigender Produktionskomplexität in Aussicht. Maschinen- und Anlagenhersteller wollen künftig durch neue Differenzierungsmerkmale, intensivierte Kundenbindung sowie durch die Sicherung und den Ausbau des Aftersales und des digitalen Services profitieren.
„Industrie 4.0“ geht hierbei deutlich über die 3. industrielle Revolution, der Automatisierung durch Computertechnologien, auch „Automatisierung 3.0“ genannt, hinaus. Grundgedanke ist, dass die Informationen und Daten nicht in einer Art „Datensilo“ an der Maschine verbleiben, sondern jeder Hard- und Software im Unternehmensnetz zur Verfügung gestellt werden. Im Gegensatz zur Automatisierung werden die Sensordaten demnach nicht nur an der Maschine oder Anlage genutzt, an der diese Informationen erzeugt werden, sondern ermöglichen neue Funktionen und Mehrwerte auch an anderen Maschinensystemen, an beziehungsweise durch Unternehmenssoftware und auf Automatisierungsebenen oberhalb der Feldbus- und Steuerungs(SPS)-Ebene. Hierfür ist es unverzichtbar, dass möglichst alle Maschinen sicher und nahtlos miteinander kommunizieren können. Diese Kommunikationsschnittstelle und aufbauende Services werden zukünftig neben den technischen Alleinstellungsmerkmalen ein wichtiges Eigenschaftsfeld für Produktdifferenzierung bilden. Gleichzeitig sind die Kommunikationsschnittstellen Voraussetzung dafür, dass im digitalen Modell, dem sogenannten „digitalen Zwilling“, ein Optimum der Produktionsprozesse für die aktuellen Randbedingungen gefunden und an die Steuerung der „Smart Factory“ übertragen werden kann.
Die „Smart Factory“ im Mittelstand
Die digitale Transformation mittelständischer Fertigungen zu sogenannten „Smart Factories“ beinhaltet viele Facetten. Insbesondere weil die Welt der kleinen und mittleren Unternehmen (KMUs) so vielfältig ist, unterscheiden sich die eingesetzten Maschinen, Logistiksysteme, Produktionsprozesse und Softwaresysteme von Fabrik zu Fabrik. Grundlage der „Smart Factory“ sind die sogenannten „Assets“, die miteinander vernetzt werden sollen. Dies können zum Beispiel Maschinen, Vorrichtungen oder Komponenten in der Fabrik sein. Jedoch können auch weitere Bereiche des Unternehmens, wie Gebäudesteuerung oder Zutrittskontrollen, oder Prozesse außerhalb des eigenen Unternehmens, zum Beispiel Lieferanten, mit einbezogen werden.
Das Ziel ist es, anhand der Digitalisierung und Vernetzung wichtige Wettbewerbsfaktoren, zum Beispiel Flexibilität, Termintreue, Qualität oder Kundenzufriedenheit, zu erhöhen und neue, innovative Geschäftsmodelle zu ermöglichen.
Struktur und Umfang des digitalen Netzwerks einer „Smart Factory“
Voraussetzungen für die „Smart Factory“ schaffen
Bevor die Vorteile einer „Smart Factory“ genutzt werden können, muss eine Computerisierung und Vernetzung aller Maschinen in der Fabrik gegeben sein. Moderne Maschinen haben in den meisten Fällen bereits ein digitales Steuerungssystem (zum Beispiel speicherprogrammierbare Steuerungen (SPS), computernumerische Steuerungen (CNC)), das die Sensordaten ausliest und die Aktoren ansteuert. In vielen Unternehmen werden jedoch auch Maschinen genutzt, die bereits Jahrzehnte alt sind und noch stets einen guten Dienst verrichten. Solche Maschinen gilt es, mit passenden Retrofit-Lösungen zu modernisieren, sodass zumindest grundlegende Daten in digitaler Form zur Verfügung stehen.
Schritt für Schritt zu „Industrie 4.0“ (basierend auf acatech Studie: Industrie 4.0 Maturity Index)
Um die Daten aller Maschinen und Einrichtungen in einer „Smart Factory“ nutzen zu können, müssen diese über eine geeignete Konnektivität (Anschlussmöglichkeit) verfügen. Klassischerweise kommen heute in der Automatisierungstechnik Feldbussysteme zur Produktionssteuerung zum Einsatz. Mit diesen wird beispielsweise der Produktionsablauf gesteuert oder das Zusammenspiel mehrerer Maschinen koordiniert. Die Nachteile vieler dieser Bussysteme für die „Smart Factory“ liegen jedoch in ihrer geschlossenen Architektur, der fehlenden Interoperabilität verschiedener Systeme (Interoperabilität = Möglichkeit, nahtlos zusammenzuarbeiten) sowie der Kapazitätsbeschränkung für das enorm wachsende Datenaufkommen. Für eine „Smart Factory“ müssen daher offene Schnittstellen, zum Beispiel OPC UA, an den Maschinen und Anlagen eingesetzt werden. Wenn die bestehenden Steuerungen dabei nicht angepasst werden sollen oder diese die benötigte Rechenleistung nicht haben, ist es empfehlenswert, externe Gateways (Vermittlungsgeräte bei Rechnernetzen) mit entsprechenden Protokolladaptern zu nutzen, die die Steuerungsdaten auslesen, diese zu relevanten Informationen weiterverarbeiten und der „Smart Factory“ zur Verfügung stellen. Bei einigen am Markt erhältlichen Lösungen für Hardware-Gateways ist jedoch zu beachten, dass diese zwar die Sensordaten auslesen, diese dann aber an ihre eigene Cloud weiterleiten und dort dem Kunden zur Verfügung stellen. Da diese Cloud nicht in der Hand des Kunden, sondern in der des Gateway-Anbieters ist, führt eine solche Lösung zu einer unerwünschten Abhängigkeit von der Cloud und schränkt die Flexibilität erheblich ein.
Aktuelles sehen, Vergangenes verstehen, Zukünftiges vorhersagen
Wenn diese Voraussetzungen im Unternehmen geschaffen wurden, zeigen sich die ersten Mehrwerte bereits durch das jederzeit aktuelle, digitale Abbild der Fertigung. Dieser neue Blickwinkel liefert ein transparentes Bild von Ursachen und deren Wirkung. Entscheidend ist dabei im Vergleich zu Einzellösungen, dass die Sichtbarkeit und Transparenz alle digital angebundenen Maschinen umfasst. So können dem Fabrikbetreiber beispielsweise auf einen Blick die anstehenden Wartungstermine aller seiner Maschinen angezeigt werden. Die bisher nötige Zusammenführung von Einzeldaten und die manuelle Verwaltung bleiben ihm somit erspart. Durch geschickte Planung und Zusammenlegen der Wartungen können dabei unnötige Produktionsstillstände vermieden werden.
Schafft man im nächsten Schritt durch zusätzliche Intelligenz die Fähigkeit, die Produktion zu analysieren und gesicherte Vorhersagen zu treffen, lassen sich erhebliche Effizienzgewinne erzielen. Unternehmen sind damit in der Lage, Entscheidungen rechtzeitig zu treffen oder nötige Reaktionsmaßnahmen frühzeitig einzuleiten. So kann zum Beispiel anhand des aktuellen Verbrauchs der nötige Zeitpunkt für eine Gaslieferung bestimmt werden, oder der Endkunde kann frühzeitig auf eine Verzögerung seiner Bauteile aufgrund eines Produktionsproblems hingewiesen werden.
Der letzte Schritt beschreibt die Zukunftsvision einer „Smart Factory“ mit sich selbst organisierenden Produktionsressourcen, die als Assistenzsysteme die Produktionssteuerung unterstützen und auf sich ändernde Randbedingungen reagieren können. Wenn die hier bereits beschriebenen Voraussetzungen geschaffen sind, lässt sich bereits heute ein gewisser Grad an Autonomie in der Fertigung umsetzen. Je nach Maschinenkomplexität und Verfügbarkeit können beispielsweise bei einem Maschinenausfall automatisch eine Reparatur angefordert, der Produktionsprozess auf andere Maschinen verlagert und eine Veränderung der Produktionsreihenfolge vorgeschlagen oder direkt vorgenommen werden.
Somit bietet eine intelligente, herstellerübergreifende Vernetzung der Fertigung eine bisher nicht vorhandene Transparenz und bildet damit die Grundlage, um effizient zu produzieren, Ressourcen zu sparen und das Unternehmen zu steuern. Aber am wichtigsten ist: Dies ermöglicht es KMUs, die Wettbewerbsfähigkeit trotz sinkender Losgrößen und steigendem internationalen Wettbewerb künftig zu sichern.
Anwendungsbeispiel Plasmaschneidmaschine
Um neue Maschinen ohne großen Aufwand zukünftig direkt in eine „Smart Factory“ einbinden zu können, sind deren Konnektivität und die digitale Datenverfügbarkeit eine essenzielle Grundvoraussetzung. Im Folgenden wird dies am Beispiel einer Plasmaschneidmaschine verdeutlicht, und es werden Anwendungsvorteile und Mehrwerte zusätzlicher digitaler Services beschrieben.
Plasmaschneidmaschinen gestatten in Verbindung mit einer CNC-Brennschneidmaschine und entsprechenden Absauganlagen das Schneiden von Metallen im Blechdickenbereich von 0,5 mm bis 160 mm. Moderne Plasmaschneidmaschinen stehen hierbei für hohe Schneidgeschwindigkeiten und einen nahezu nachbearbeitungsfreien Schnitt. Neben den Kosten der Plasmaanlage und der Verschleißteile sind vor allem die Schnittqualität und die Schneidgeschwindigkeit konventionelle Produktunterscheidungsmerkmale. Bei den Plasmaschneidanlagen der neuen „Q-Serie“ werden diese von digitalen Eigenschaftsfeldern erheblich erweitert.
So sind bei der neuen „Q 3000“ sowohl die Maschine als auch die Gasbox und die Brenneranschlusseinheit mit Microcontrollern ausgerüstet, die sich gegenseitig erkennen und Prozess- und Zustandskennzahlen für die zentrale Steuerung bereitstellen. Diese verwendet die Daten in einem Modell für interne Analysen und hinterlegt die Daten in einer Datenbank. Die Steuerung berechnet unter anderem die Restlebensdauer elektrischer Bauteile und der Plasmaanlage, summiert den Strom- und Gasverbrauch und kann auf mögliche Fehlbedienungen schließen. Die Informationen werden entweder (in geringerem Umfang) über das Feldbussystem „EtherCAT“ an die CNC-Maschine weitergegeben oder können über Ethernet aus dem Netzwerk abgerufen werden. Hierbei wurden drei Kommunikationsebenen konzipiert.
Kommunikationsebenen einer Plasmaschneidanlage
Die Bedienerschnittstelle zielt auf die Unterstützung des Maschinenbedieners. Die Informationen werden durch eine Webanwendung bereitgestellt, die über verschiedene Endgeräte, zum Beispiel Tablet, Personalcomputer oder Handy, mit einem Webbrowser abgerufen beziehungsweise sichtbar gemacht werden. Unter anderem werden Parametersätze unterschiedlichen Schneidaufgaben zugewiesen und die hierfür zu bestückenden Verschleißteile eindeutig benannt und visualisiert. In der Webanwendung sind weiterhin die Betriebsdokumente und Videos zur Fehlerbehebung sowie Wartungs- und Bedienungsanleitungen hinterlegt und mit Fehlermeldungen der Maschine verknüpft. Der Strom- und Gasverbrauch kann durch eine Kalenderfunktion nachvollzogen werden.
Die Informationen können weiterhin dem Maschinennetzwerk zur Verfügung gestellt werden. Dort lassen sich zum Beispiel die Informationen zum Wartungszustand und zu der Restlebensdauer der CNC-Brennschneidmaschine in die Predictive-Maintenance-Funktionen (predictive maintenance = vorausschauende Instandhaltung) der Gesamtanlage integrieren. Andererseits können Zustandsdaten der Maschine direkt zur Ansteuerung anderer Maschinen verwendet werden, zum Beispiel von Absaugmaschinen oder Lüftungsanlagen zur Minderung von Strom- und Heizkosten. Letztlich können Informationen zum Strom- und Gasverbrauch eindeutig Kostenstellen oder Produkten zugeordnet werden und ermöglichen ein präziseres Monitoring der Maschinenkosten (Total Cost of Ownership) und der produktbezogenen Herstellkosten.
Letztlich lässt sich mit einem in der Maschine integrierten Router und mit ausdrücklicher Zustimmung des Anlagenbetreibers eine Verbindung mit dem Kundendienst des Maschinenherstellers aufbauen. Dieser hat online und ohne zusätzliche Reisekosten die Möglichkeiten:
- mit dem Anlagenbetreiber gemeinsam den Prozess oder die Funktionalität der Maschine zu monitoren,
- auftretende Anwendungsprobleme bis in die interne Kommunikation der Plasmaschneidanlage zu analysieren und Anpassungen vorzunehmen,
- den Softwarestatus zu aktualisieren, um zum Beispiel mit Software Updates neue Hilfe-Videos und Tutorials oder Parameteranpassungen zur Verlängerung der Lebensdauer von Verschleißteilen zu installieren.
„Industrie 4.0“ – vom Mittelstand für den Mittelstand
„Industrie 4.0“ bietet vor allem dem Mittelstand durch herstellerübergreifende Zusammenarbeit auch im globalen Wettbewerb erhebliche Chancen. Trotzdem haben 80% aller KMUs in Europa bisher noch keine umfassenden Schritte unternommen, um die Vernetzung in der eigenen Fertigung oder die ihrer Produkte voranzutreiben. Dies liegt vorwiegend an der Angst vor hohen Kosten, vor Abhängigkeit von einem Anbieter sowie fehlenden Kapazitäten, um sich mit dem Thema detailliert auseinanderzusetzen. Zudem haben viele KMUs keine spezifizierte Umsetzungsstrategie und drohen im internationalen Digitalisierungswettlauf den Anschluss zu verlieren.
Um mittelständische Unternehmen bei der Digitalisierung ihrer Produkte und Produktion zu unterstützen und herstellerübergreifende Lösungen mit handfestem Mehrwert für Kunden gemeinsam zu entwickeln, wurde 2016 der Verband Industry Business Network 4.0 e. V. ins Leben gerufen. Neben mittelständischen Herstellern aus dem Maschinen- und Anlagenbau zählen der TÜV Süd sowie das Fraunhofer IGCV zu den Gründungsmitgliedern und stellen den Mitgliedern ihre Expertise und Beratung zur Verfügung. In dem Verband arbeiten zahlreiche technologieführende Maschinenhersteller, Dienstleister und Anwender daran, Produkte für „Industrie 4.0“ zu entwickeln und diese an realen Referenzanlagen in Technologiezentren und in der Produktion zu testen. Mit der hierzu gestarteten Initiative „IndustryFusion“ lässt der Verband die offene, herstellerübergreifende und nahtlose Vernetzung – also den Kerngedanken von „Industrie 4.0“ – Wirklichkeit werden. Auf Basis einer herstellerübergreifenden Open-Source-Vernetzungslösung für „Smart Factories“ ermöglicht „IndustryFusion“ eine nahtlose Verknüpfung von Maschine, Fabrik und gegebenenfalls Cloud-Plattformen. Die Einfachheit der Umsetzung ist dabei zentraler Bestandteil der Lösung und befähigt somit besonders KMUs, die Vorteile eines breiten „Industrie-4.0“-Ökosystems zu nutzen.
Der erste wichtige Meilenstein wurde auf der Messe „EuroBlech“ 2018 in Hannover präsentiert. Getreu dem Messemotto „Am Puls der Digitalisierung“ wurden über mehrere Messestände hinweg mehr als 20 unterschiedliche Maschinen und Geräte verschiedener Hersteller miteinander vernetzt und deren Informationen, beispielsweise hinsichtlich Maschinenstatus, Energieverbrauch und Wartung, nahtlos miteinander ausgetauscht und dem Besucher transparent dargestellt. Am Verbandssitz im bayerischen Bad Wörishofen wurde im Rahmen des Fachkongresses „Fertigung 4.0“ dann die erste dauerhafte Referenzanlage des Verbands in Betrieb genommen, die sich im Sinne eines lebendigen Demonstrators stetig weiterentwickelt. Weitere Referenzanlagen mit unterschiedlichen Maschinen- und Softwarekonstellationen baut der Verband derzeit an verschiedenen Standorten in Europa auf. Das so entstehende Netzwerk können die Mitglieder, aber auch interessierte Unternehmen nutzen, um sich über die Fortschritte zu informieren und aktiv an einer Umsetzung von „Industrie 4.0“ vom Mittelstand für den Mittelstand mitzuarbeiten.
Präsentation der digitalen Referenzanlage am Fachkongress „Fertigung 4.0“
Um die Leistungsfähigkeit und die Nachhaltigkeit einer offenen Vernetzung der Fertigung auch in der realen Produktion unter Beweis zu stellen, setzt der Verband seine Lösung in einem Referenzprojekt bis Ende 2020 zudem bei einem sehr innovativen Schweizer Stahlhändler mit sechs Fertigungsstandorten um. Der besondere Innovationsfaktor des Projekts liegt in der Zusammenarbeit aller beteiligten Maschinenhersteller, von IT-Experten aus dem Open-Source-Bereich, Anbietern von Softwarelösungen für den Anwender sowie dem Betreiber der Fertigung. Gemeinsam werden mehrwertbringende Anwendungsbeispiele definiert, auszutauschende Daten festgelegt und neuartige digitale Services erprobt. Somit entsteht eine Win-win-Situation für alle Beteiligten, die sich auch für die anderen Verbandsmitglieder auf die eigenen Produkte übertragen lässt.
Bei allen Umsetzungen von „Industrie 4.0“ ist es zudem wichtig, nicht nur die technischen Aspekte zu berücksichtigen. Der Verband Industry Business Network 4.0 e. V. unterstützt daher seine Mitglieder mit geeigneten Leitfäden auch bei der Vorbereitung der digitalen Transformation im eigenen Unternehmen sowie durch eine Wissensvermittlung hinsichtlich geeigneter Anwendungsfälle und neuer Geschäftsmodelle.
Dieser Artikel erschien zuerst im Magazin "Der Praktiker", Ausgabe 8/2019. Hier geht es zur Website
Autoren:
- Dr. Michael Schnick, Geschäftsführer, Oscar PLT GmbH
- Volker Krink, Leiter Entwicklung, Kjellberg Technologiepark GmbH
- Dr.-Ing. Konstantin Kernschmidt, Leitung Forschung und Entwicklung, MicroStep Europa GmbH
- Igor Mikulina, Geschäftsführer MicroStep Europa und Vorstandsvorsitzender Industry Business Network 4.0 e.V.
- Matthäus Mikulina, Business Development Industrie 4.0, MicroStep Europa GmbH